Quirk Creek Plant & Field Overview
Sour Gas, Liquids & Sulphur Processing
Quirk Plant uses an amine process to separate “acid gas”, a lean oil refrigeration process to separate natural gas liquids, and a Claus process to catalytically promote the reaction of H2S with Sulphur Dioxide to create elemental Sulphur. The Quirk Plant produces sales gas, sulphur and natural gas liquids – including propane, butane, pentane and condensate.
- Inlet Separation:
Sour gas entering the Plant is “three phase” separated into sour gas, hydrocarbon liquids and water. Gas is com¬pressed in large reciprocating gas compressors. - NGL Stabilization:
Natural gas liquids (NGL’s) are stabilized, to meet pipeline sales specifications, by removing the H2S, methane and ethane. NGL’s consisting of propane, butane, pentane and other heavier hydrocarbons are pumped from the plant through a proprietary 55km pipeline across the TsuuT’ina Nation to infrastructure owned by Plains Midstream. - Gas Sweetening:
Sour gas from the inlet separators and stabilizer system is sweetened in an amine sys¬tem by extracting H2S and carbon dioxide (CO2) (collectively “acid gas”), that is concentrated and sent to the sulphur plant create liquid Sulphur using three of the largest plant towers and associated vessels.
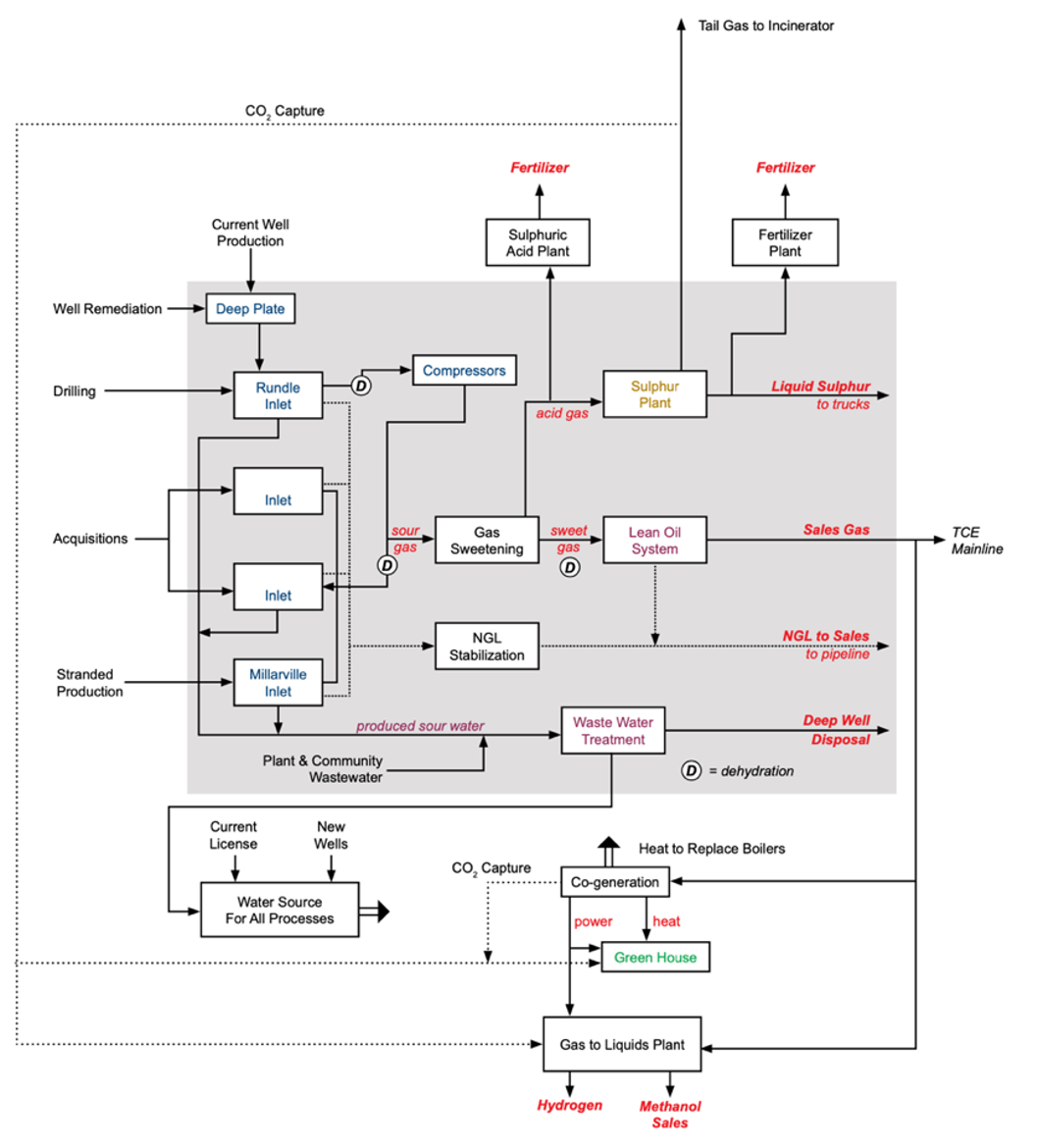
Simplified Plant Process Diagram (Current & Proposed)
- Hydrocarbon Recovery:
“Sweet” gas from the amine system flows through the lean oil system where it is refrigerated using propane and processed to remove 79% of the remaining hydrocarbon liquids that are combined with the NGL’s that were removed in the stabilizer. The lean oil system uses a heavy hydrocarbon that is circulated in the stripping tower to remove the liquids much the same way that amine is used to remove H2S gas. This system has a “best in class” recovery efficiency of 79%. - Dehydration:
Trace water is removed from the sales gas using Glycol, which is regenerated for reuse. - Sulphur Production:
The acid gases, containing H2S (67%) and other sulphur compounds are converted to liquid sulphur in the sulphur plant using a “Claus” process, a three-stage, sub dew point, MCRC. The acid gas mix¬ture is burned with large amounts of air to generate high tem¬peratures of 1200 C (2192 F) for the sulphur re¬actions to occur with minimal tail gases, achieving sulphur plant efficiency in excess of 99%, world class, despite the Plant’s 50 year age. The tail gases that remain, consisting of Carbon Dioxide, Sulphur Dioxide and water are incinerated in a 107 meter (350 foot) in¬cinerator stack. The stack top temperature is maintained at 450 C (842F) which is closely monitored so that the air emissions are as low as possible, thus enabling optimum sulphur recovery and ensuring we meet and exceed our air license, with the Alberta Government. The Sulphur is trucked in molten form to a local rail terminal where it is shipped to domestic and world markets primarily for fertilizer markets. - Control Systems:
The Plant and field facilities are controlled by a central computer or Distributed Control System (DCS) that controls key portions of the plant by maintaining proper temperatures, pressures and flow rates ensuring plant safety and efficiency.